
WHAT IS CWT
CWT is an indirect heating system that is designed to heat crude oil for processing purposes.
CWT patented technology uses steam to indirectly heat crude oil, making it much safer, more cost effective, and better for the environment than the traditional firetube systems that are currently used today.
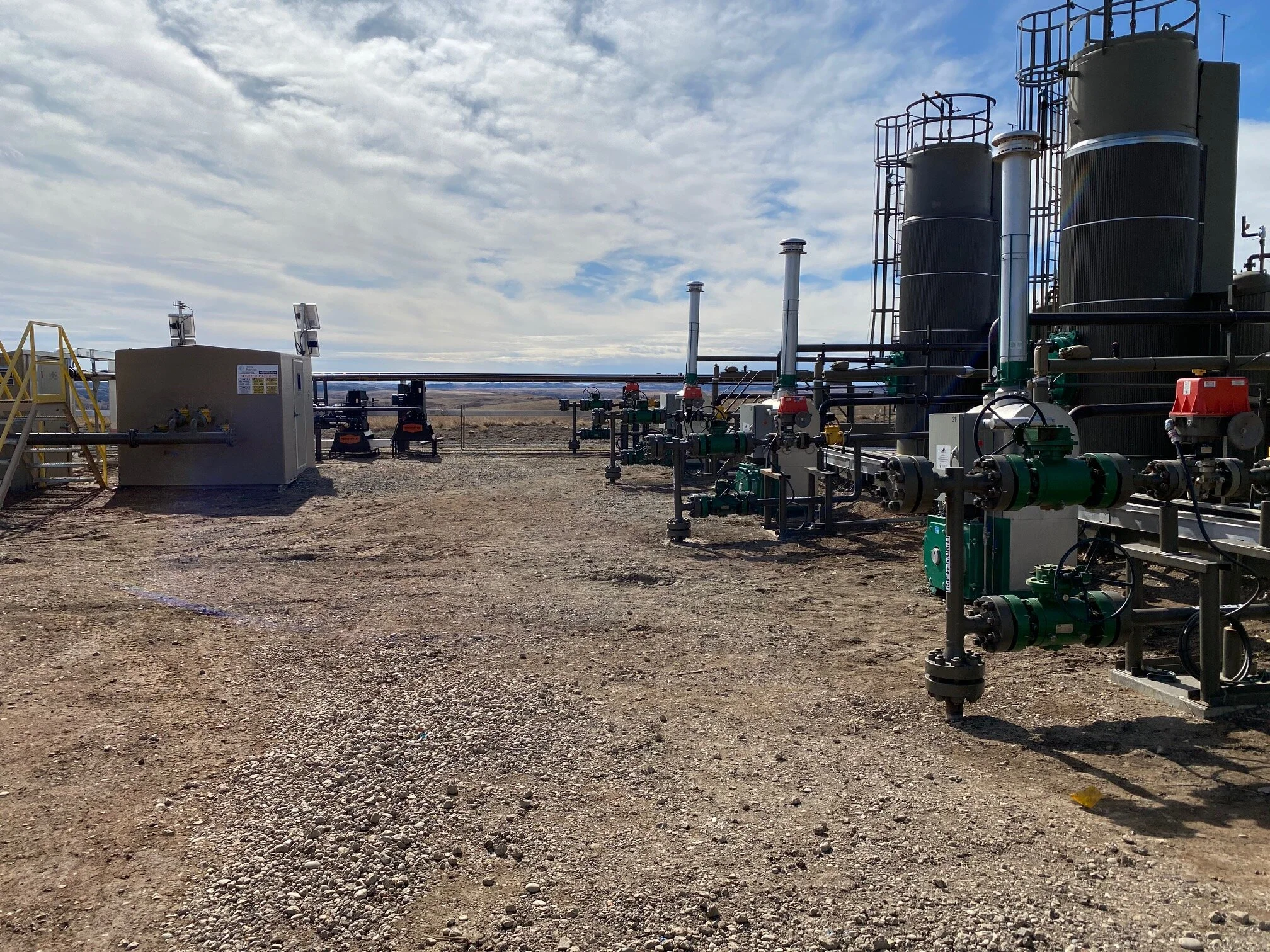
HOW CWT WORKS
The CWT indirect heating system is a two-phase thermosiphon that transfers heat to the process through an innovative technology called the Heat Driven Loop (HDL).
A mixture of water and glycol is contained in a vacuum state and heated by a low-pressure flame bed. The water changes to steam at a lower temperature due to the vacuum state.
The steam is then allowed to rush towards the process which requires the heat through a system of tubes (heat exchanger). The steam then expends its energy and condenses back to liquid form.
The liquid (Water) then gravity feeds back to the evaporation chamber where it will again be recharged back to steam.
This continuous loop of transferring energy from a flame bed to process fluid, using steam and the latent heat of vaporization, is the key to the CWT system.
CWT: THE PROCESS SYSTEM
Utilizes an ASME Sec IV steam boiler
Closed system under vacuum with no make-up water
Low pressure flame bed supplies heat to the water/glycol mixture causing the water to boil almost instantly which results in an exceptional response time
Uses a process line temperature sensor ensuring exact control
Steam temperature self-adjusts up to 250F
Uses the latent heat of vaporization making it more efficient
ASME Sec IV controls ensure safety
SEE THE BENEFIT OF GREEN TECHNOLOGY
Benefit of CWT Indirect Heating vs. Traditional Firetube Methods
One of the components of CWT indirect heating system is the Heat Exchanger. The steam coils of the heat exchanger can be submerged directly in the oil emulsion area. This allows oil producers to lower the water-oil interface level in the treater, which will allow for greater treater capacity and the ability to treat more oil.
CWT Heat Exchanger
Another added benefit to the CWT system is that by utilizing steam through the heat exchanger coils we do not see the high skin temperature and scale build up that you would see using a firetube. With no scale build up on the steam coils, you have true consistent heat transfer throughout the exchanger. Resulting in an increase in efficiency, longer life of the exchanger along with reduced operator and maintenance costs.

Not a question of If you will have a firetube failure, but a question of When.
REMOVE THE RISK AND ELIMINATE FIRETUBE FAILURES WITH THE TECVALCO CWT INDIRECT HEATING SYSTEM.
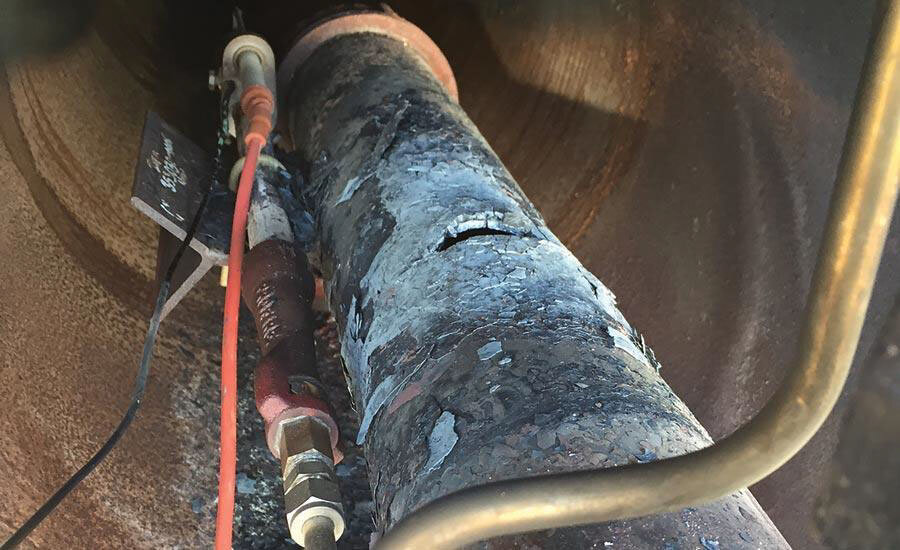
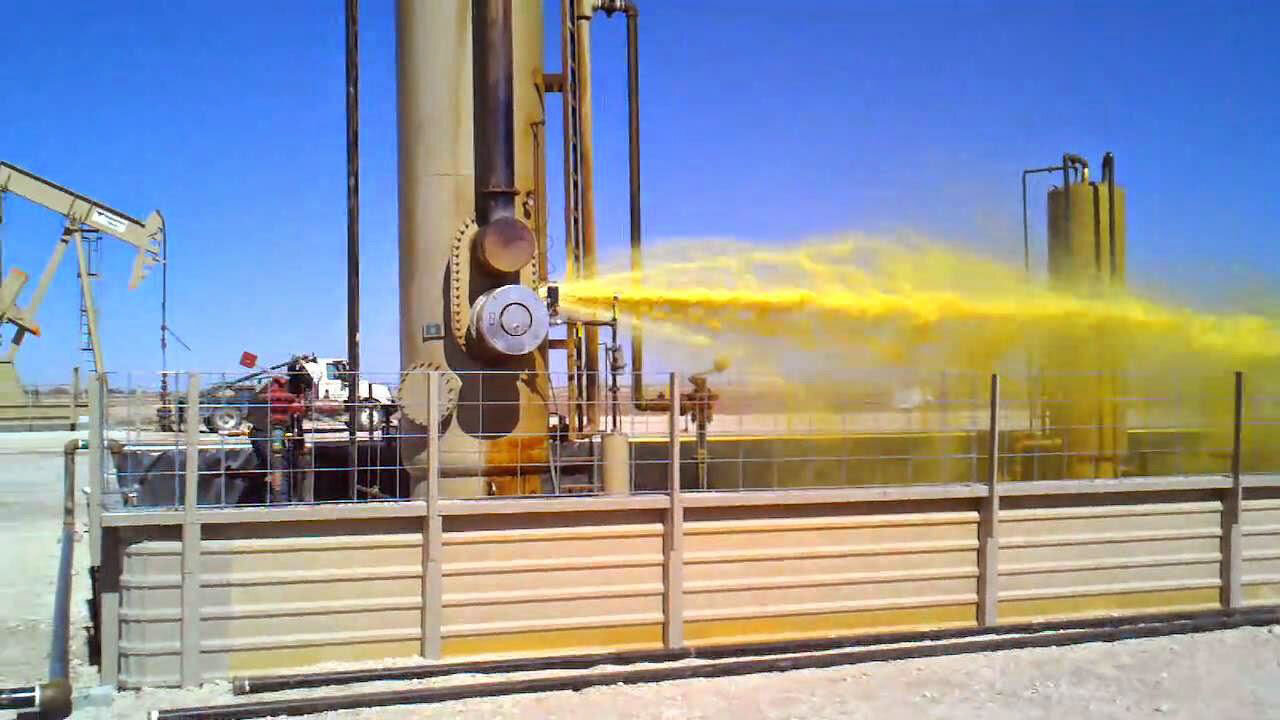
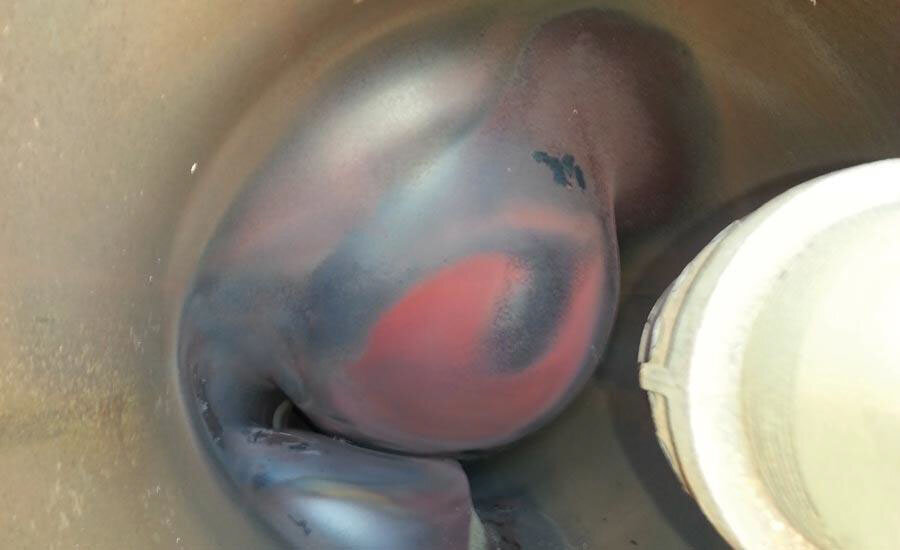
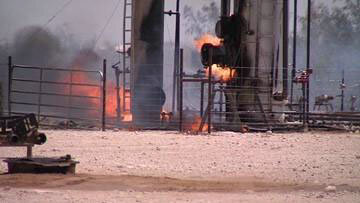
OPERATOR INITIAL SERVICE INSPECTION
CWT Exchanger
CWT Exchanger pull after 2-1/2 years of service for inspection. Heat exchanger green coating was unharmed and looked the same as it did when it was first installed into the treater.
Firetube
Firetube after less than two years of service. Notice all of the corrosion and heat degradation to the tube. This will most certainly end with a firetube failure.
CWT HEAT EXCHANGER vs. FIRETUBE
CWT Heat Exchanger New Technology
Purpose designed for tank and treater applications
ASME Sec VIII flange and tubes
Approved for use in the US & CA
Standard models with 112 ft² and 149 ft² of tube transfer area (will replace 0.5 mm btu/hr and 1.0 mm btu/hr fire tubes)
Uses latent heat transfer (condensing steam) yielding a uniform temperature profile across the entire exchanger
Multiple tube arrangement utilizes a larger x-sec area of the vessel (16 5/8” wide), yields superior heat distribution
Relatively low volumetric displacement of fluid for given heat transfer rate (5.5 ft3 for 6x20 treater)
Firetube Traditional Method
Poor thermal efficiency (industry studies indicate 40-45% at best)
Hot section is subject to extreme temperatures and direct flame impingement
High temperatures cause premature gasket failures
High skin temperatures mean that the oil cannot be in direct contact with the tube, must heat the water phase (increases vessel size)
High temperatures cause the water in contact with the firetube to boil which leads to tube scale (mineral deposits)
Tube scale reduces heat transfer and results in increased localized skin temperatures and tube degradation
High temperatures reduce the life of corrosion inhibiters (coatings)
Reduced heat transfer requires increasing the firing rates, which compounds the problems
Tube failure is imminent
REDUCE YOUR OVERALL ENVIRONMENTAL IMPACT
Heater Gas Consumption
The CWT indirect heating system has a major increase in thermal efficiency. The CWT system boasts thermal efficiency between 70 and 80 percent. (third-party tested) With the CWT system running on low pressure of (2oz) of well head or utility gas the CWT system has a reduction of fuel gas consumption by up to 50 percent and the increase in thermal efficiency means that there is less fuel consumption and less greenhouse gas emissions emitted to the atmosphere.
Vacuum State HDL
The vacuum state that the CWT system runs on also reduces corrosion as there is very little to no oxygen inside the heat driven loop (HDL) system and allows the heater to operate at less than 15PSI and as high as 250F.